The aviation industry is constantly evolving, and the EcoPulse project is a clear example of how technological innovation is driving a more sustainable and efficient future. This demonstrator, a distributed hybrid propulsion aircraft, was jointly developed by Airbus, Daher, and Safran—three giants in the aerospace industry. The results of the flight tests, conducted between November 2023 and July 2024, suggest a promising future for hybrid-electric aviation.
What is EcoPulse?
EcoPulse is a demonstrator based on the Daher TBM 900 turboprop aircraft, modified to evaluate the potential benefits of distributed hybrid-electric propulsion. This system distributes thrust generation among multiple small engines located along the wings, which could improve aircraft performance, particularly in terms of cabin noise reduction and energy savings.
The project was divided among the three partners according to their areas of expertise: Safran was responsible for developing the hybrid-electric propulsion system, including the six e-propellers mounted on the wings. Airbus Defence and Space contributed an 800-volt high-energy-density battery, capable of delivering 350 kilowatts of electricity—enough to power the six e-propellers during flight. Additionally, Airbus developed the flight control system and managed the aerodynamic and acoustic integration of the propulsion system. Meanwhile, Daher integrated the modifications from Airbus and Safran into the fuselage and oversaw all flight testing and certification.
→ This is how the Airbus A350F is built: Tools, Technology, and Industrial Challenges
Key Flight Test Results
The EcoPulse flight test program lasted eight months, during which 50 flights were conducted, accumulating approximately 100 flight hours. These tests examined various aspects such as aerodynamics, energy efficiency, noise, and flight control. The results were mostly positive, highlighting significant advancements in several key areas.
1. A Leap Forward in Battery Technology
One of the most remarkable aspects of the project was the development of an 800-volt lithium-ion battery, specifically designed for EcoPulse. This battery, developed internally by Airbus Defence and Space, represents a major breakthrough, as standard aviation batteries are typically low-voltage and low-energy-density, mainly intended to power the auxiliary power unit (APU) or for emergency use.
Christophe Robin, Chief Aircraft Designer at Daher, explained the importance of this innovation: “Normally, in a light aircraft, we use a 28-volt battery. In a commercial aircraft, the standard is 115 volts AC. What we are using here [in EcoPulse] is 800 volts [DC], and that’s a completely different story.” During the tests, the battery control models were successfully validated, demonstrating that a battery of this power can be safely integrated into an aircraft without compromising safety standards.
2. Wing Aerodynamics Improvements
The tests confirmed that distributing thrust to the e-propellers positioned closer to the wing tips reduced aerodynamic drag during cruise, leading to greater energy efficiency. Jean-Baptiste Manchette, Head of Propulsion of the Future at Airbus, emphasized: “Using electric power to understand wing behavior and how we could enhance lift, reduce takeoff distance, and use it in climb and cruise was a great result.”
3. Innovative Flight Control Testing
EcoPulse also tested an innovative flight control system that used asymmetric thrust generated by the e-propellers to yaw the aircraft (replacing the rudder) and roll it (instead of using ailerons). Test pilots reported that the target roll rates were achieved and that maneuverability was positive. Thibaud Brouze, one of Daher’s test pilots, commented: “It was really interesting to fly with the fly-by-wire system and control yaw and roll through the flight computer… it was very exciting to fly such an uncommon aircraft.”
4. Noise Reduction and Perception Tests
Noise tests, both external and internal, showed that the e-propellers, which rotated at different speeds to improve aerodynamics or control flight, generated a distinct noise compared to conventional propellers. However, cabin technologies used in traditional propeller-driven aircraft—such as acoustic dampers and synchro-phasing (controlling blade speed and synchronization of the e-propellers)—were also effective in reducing decibel levels inside the EcoPulse cabin.
5. Enhancements in Digital Modeling
A digital twin of the entire aircraft was created to predict its behavior, including submodels for key technologies such as the electric propulsion system, battery, and flight controls. The data collected during the tests was integrated into this digital twin, improving its accuracy. This advancement will be crucial for designing future aircraft incorporating these technologies.
The Future of Hybrid-Electric Aviation
The results of EcoPulse will have a significant impact on aircraft design at Airbus. Jean-Baptiste Manchette stated: “This EcoPulse campaign allows us to advance certain hybrid-electric technologies, such as high-voltage batteries, and integrate them into future aircraft, helicopters, and urban air mobility solutions.” He also highlighted that distributed electric propulsion enabled them to model flight physics and energy management at the aircraft level—key elements for the next generation of airplanes.
The collaboration between Airbus, Daher, and Safran does not end here. Daher and Safran are working on a joint project, while Airbus and Safran (through Safran’s 50% stake in CFM International) are exploring the feasibility of open-fan engines via the RISE demonstrator. As Jean-Baptiste put it, “Testing things in flight is where you really learn a lot,” and Christophe Robin added, “Real conditions never lie.”
Related Topics
Boeing Negotiates Sale of Up to 500 Aircraft to China
Airbus A320 is About to Break a Record Held by Boeing 737 for Decades
Boeing Deliveries Drop 20% in July Compared to June: Airbus Maintains Lead
Boeing Faces a New Era: Kelly Ortberg Stabilizes Aerospace Giant but Faces Key Challenges
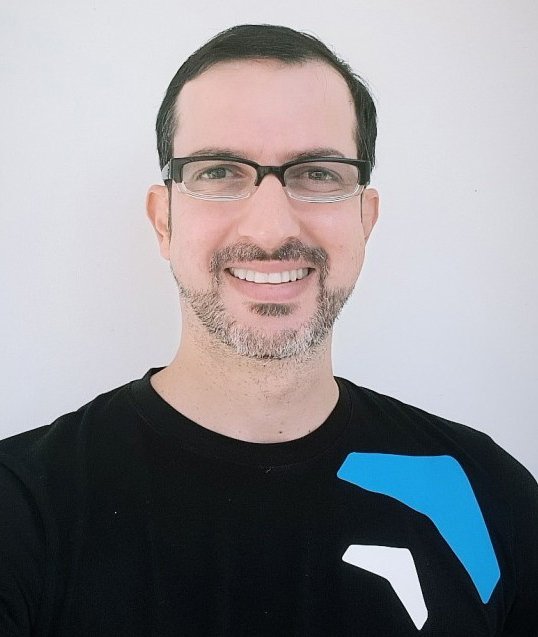
Un apasionado por la aviación, Fundador y CEO de Aviación al Día.